
Bentonite - natural clay material. Use is very diverse. Compared to powdered bentonite, Granular bentonite has a higher logistics efficiency and a lower risk of dust pollution. So, how to produce bentonite pellets? This can be achieved using granulator bentonite. We have two -wool bentonite granulators, disk bentonite granulators and drum bentonite granulators, which will help you produce bentonite granules. Thanks to thorough design and innovative technologies, our granulatory equipment can adapt to your needs at various production scale. Ensuring that, so that your final product corresponds to market expectations or exceeds them. Whether it is quality or performance.
How to choose a granutonite granulator suitable for you in accordance with the granulation process?
There are two methods of granulation of bentonite: Dry and wet. The most common type of dry granulation of bentonite is a two -piece granulator. Wet granulation of bentonite includes a disk granulator and a drum granulator. If you choose the process of dry granulation, You can choose a roller granulator for the production of bentonite granules. This is widely used equipment for dry granulation. It is characterized by low energy consumption, simple technological scheme and the possibility of continuous production. High performance. You can provide stable product quality, accurately monitoring the size and shape of bentonite particles.
Do we have to choose a disk granulator or drum granulator for a wet granulation process? The drum granulator is suitable for large -scale production of bentonite granules. The maximum performance of the drum granulator can reach 30 tons/time. If you produce large -scale production, You can choose a drum granulator. The disk granulator is suitable for the production of bentonite granules of small and medium sizes. Its cost is much lower, than the eardrum. So, If you have a limited budget or small scale, You can choose a disk granulator for the production of bentonite granules.
What granulation processes can you use for granulators of bentonite?
Conventional granulation processes of bentonite include the process of dry granulation and the process of wet granulation. You can choose depending on your situation.
Dry extrusion granulation is an effective method for processing bentonite. He uses physical pressure to direct compression of powder raw materials in particles of the desired shape. Bentonite granulator uses this method to complete the granulation of bentonite. Bentonite powder is supplied to equipment with a minimum addition of moisture or without it. Due to powerful extrusion of rolls, the powder is compacted under high pressure and is formed in particles. Then the granules are crushed and sifted to achieve a homogeneous size and shape. The advantage of dry extrusion granulation is, that you do not need to perform the subsequent stage of drying. He is energy -saving, has a low thermal sensitivity to the material and can maintain the initial properties of your bentonite products.
Wet granulation is a process, in which the corresponding amount of fluid is added to the bentonite powder (usually water or special binder). This added liquid acts as a binder, Creating a connection between the particles of the powder with the formation of larger particles. The usually used equipment includes a disk granulator and a drum granulator. Bentonite wet material is gradually condensed from small powder to larger particles under the influence of centrifugal force in granulation equipment. However, you will need to go through the drying process, to remove excess moisture from bentonite granules and ensure the hardness and stability of granules. Thanks to the process of moist granulation of bentonite, you can better control the size of the particles and receive ready -made granules of higher strength.
Our granulators for bentonite can produce granules which size?
Our granulators for bentonite can produce granules of various sizes. Each granulator type has its advantages. You can choose the most suitable granulator depending on your requirements for the size and density of granules of bentonite to achieve production goals. Our granulators for bentonite can offer the following solutions for granules:
The disk granulator is usually suitable for the production of granules with diameter from 2 to 20 millimeters. By adjusting the angle of inclination and the speed of rotation of the disk, you can control the size of the granules to a certain extent. With the help of thorough tuning and control, you can achieve accurate production of small granules.
Roller (Two -roller) the granulator is usually capable of producing granules the size of 1 to 10 millimeters. The size of the granules mainly depends on the design of the matrix and the gap between the rollers. The roller granulator is usually used to produce more homogeneous and dense granules.
The drum granulator is suitable for the production of granules in a wider size range, Usually from 3 to 30 millimeters. Adjusting the speed of rotation of the drum and the time of stay of the material allows you to change the size of the granules. Although drum granulators for bentonite in most cases are used to produce larger granules, By adjusting the parameters of work, you can achieve smaller granules, relevant to your requirements.
What steel is used to make our bentonite granulator?
Our bentonite granulators are available in various styles. Most of them are made on the basis of carbon steel Q235, alloy steel and t. e. The use of these materials not only provides excellent strength and wear resistance, but also increases the corrosion resistance of the equipment. Besides, These materials have a smooth surface, which is easy to clean and support. This will extend the life of your equipment and reduce operating costs. We strive to provide you with effective and reliable solutions for granulation of bentonite to meet various production needs.
What are the advantages of converting powdered bentonite into a granular form using a granutonite granutonite?
Powdered transformation bentonite In a granular form using a bentonite granulator can bring you many advantages. Bentonite granules significantly improve the quality of customer service. First of all, granular bentonite has significantly improved fluidity and ease of operation. Can help you simplify the process of dosing and mixing. Reduce material losses during transportation.
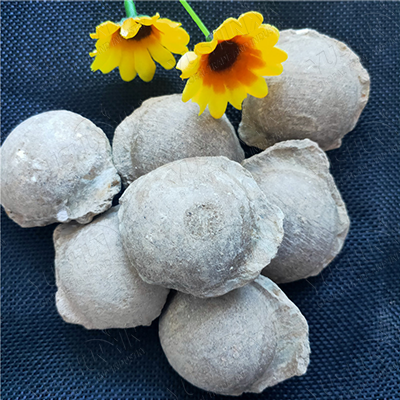
Besides, Granulation of bentonite significantly reduces dust pollution and threat to the health of operators. You can control the rate of dissolution or absorbing ability, adjusting the size of the particles, To improve your product characteristics. Moreover, You can also add other useful ingredients in the granulation process. Such as Microelements and t. e. Improve the functionality of your product even more. Increase value added and market attractiveness of your products.
What are the use of bentonite granules, which you produce using granutonite granulator?
Bentonite granules - universal material, widely used in various industries. In agriculture, it can be used as a soil air conditioner to improve air permeability and water holding of the soil. Helps plant growth. When cleaning water, a bentonite particle can be used as a floculant, helping to clean water sources.
Moreover, The water -absorbing and coagulating properties of bentonite make it the perfect material for cat toilets. Besides, Bentonite particles are widely used in drilling, construction, cosmetic and pharmaceutical industries and other industries. Therefore, bentonite particles are a very popular market in the market.
Particles of Bentonite what size in millimeters are more popular in the market?
Market demand for bentonite particles varies depending on the area of application. You can selectively produce bentonite particles in size depending on the orientation of your product in the market. Our granulator of bentonite will help you produce granules of bentonite of different sizes. For purchase, contact us.
Popular products - carriers of complex fertilizers.
Bentonite clay has several advantages as a carrier for the production of fertilizers. High adsorption properties of bentonite allow it to absorb a large amount of nutrients and moisture. Its properties of slow release allow you to effectively control the release of nutrients from fertilizers, using bentonite as a carrier, and improve the use of nutrients. Besides, Bentonite itself has a significant impact on the improvement of soil structure. It improves the maintenance of water in the soil, aeration and microbial activity. It is necessary to maintain a healthy soil environment.
How to use bentonite as a carrier for the production of complex fertilizers?
Stages of the production of fertilizers using bentonite as a carrier are actually simple. The first is the preparation and preliminary processing of raw materials, including bentonite and various nutrient raw materials. Then bentonite is crushed and sifted to the desired size and purity and mixed with nutrients, such as nitrogen, phosphorus and potassium. The mixture is subjected to the granulation process to form granules of fertilizer of a certain size and shape.
After this, the particles must be dried and cooled to increase their physical strength and stability. Then, sorting to remove unskilled particles and ensure the consistency of the product is performed. If you want to additionally control the release of nutrients and increase the efficiency of fertilizers, You can apply a moisture resistant or slowly released coating. Having completed all these steps, You can pack fertilizers and sell them.
Popular product - bentonite filler for cat toilets.
Bentonite filler for a cat toilet is a waste absorption of pets, bentonite raw material. It is widely used thanks to its excellent adsorption, coagulation and environmentally friendly properties. AND, Compared to other types of fillers for cat toilets, Bentonite filler for cat toilets, usually, has a more reasonable price. It is also a project, In which most manufacturers of bentonite granules invest. You can also Produce a bentonite filler for a cat's toilet using a bentonite granulator.
Popular products – Bentonite granular filler.
Bentonite particles are widely used as fillers in various industries. Because it has a number of unique properties. Such as high water absorption, Strong swelling, adsorption ability and ability to form. It can be used in many different applications. You can use a bentonite granulator for the production of bentonite granular fillers to meet market demand and increase competitiveness in the market.
If you have an idea to invest in a line for the production of bentonite granules, Contact us. We can provide you with professional services for the individual setting of the bentonite granules production line. Satisfy your various production scales and needs. Our line for the production of bentonite granules is designed so, To not only meet the requirements of high efficiency and environmental protection, but also ensure the quality and performance of your final product in the form of bentonite granules.
Besides, We also support the design of other decisions of production lines. For example, Ammonium sulfate granules line, Potassium chloride granules, Granular production line of phosphorus fertilizers and t. e. Welcome, Contact us!